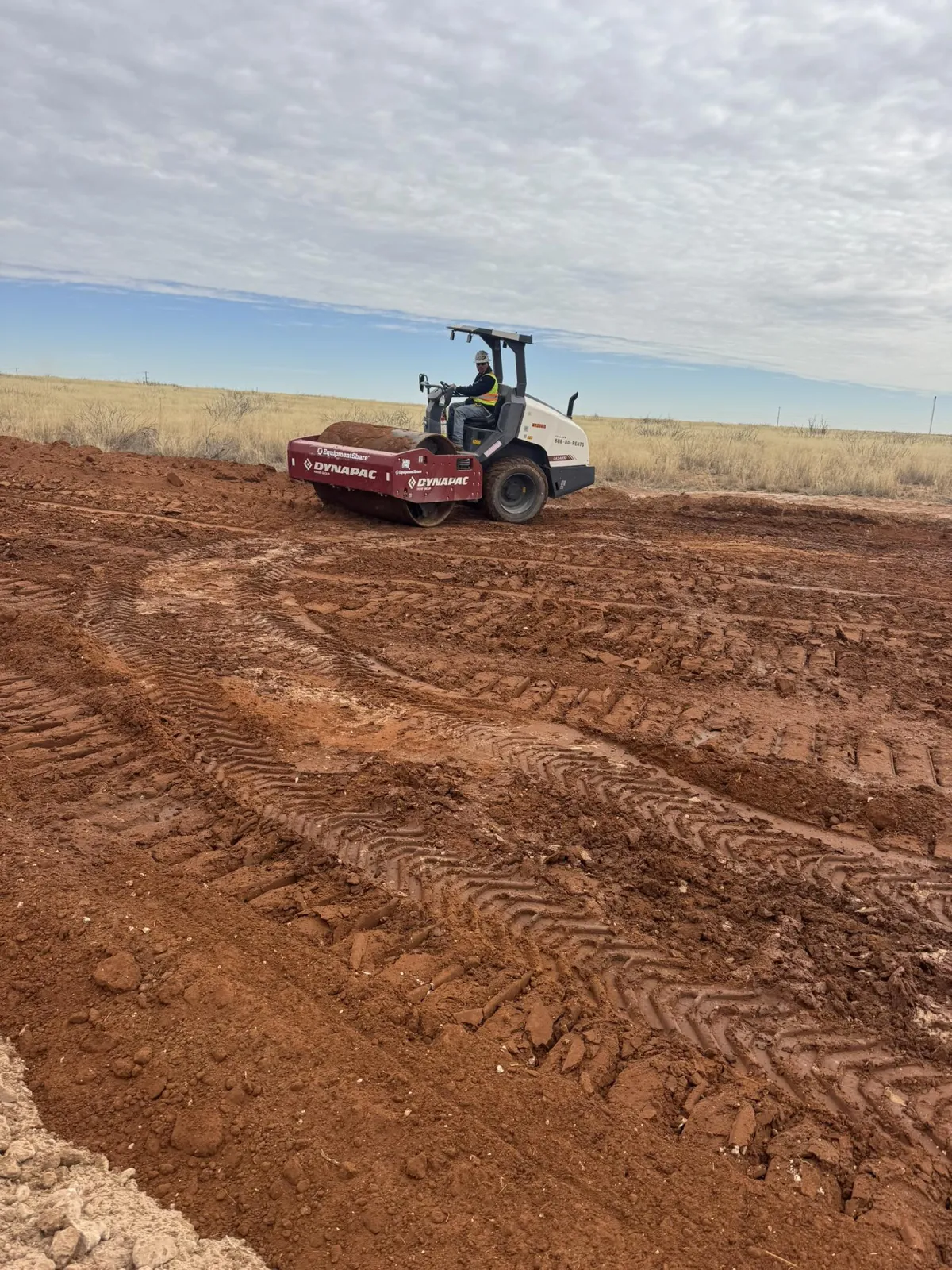
Why Soil Compaction Is Critical for Environmental Compliance in Oilfield Construction
Compact Soil and Environmental Compliance in Oilfield Construction
In oil and gas construction, what happens beneath the surface matters just as much as what gets built on top of it. One of the most overlooked yet critical factors in oilfield construction is compact soil. Whether you're laying steel and poly pipelines, building a compressor station, or preparing pad construction for drilling rigs, the way the soil is compacted directly impacts both performance and compliance.
Let’s break it down.
Why Compact Soil Matters in Environmental Compliance
Soil compaction isn't as simple as creating a solid surface to build on. In oilfield construction, it's a key player in controlling runoff, preventing erosion, and meeting regulatory requirements from agencies like the EPA.
Poorly compacted soil can allow water to seep, erode, or carry sediment into nearby waterways—a major red flag in terms of compliance. From pad construction to frac pond development, every step needs to account for how soil interacts with environmental systems.
Runoff and Erosion Control
Unstable soil is prone to erosion, especially in high-traffic areas or on sloped surfaces. When heavy rains hit a freshly cleared oilfield site, loose soil can wash away, bringing pollutants along for the ride. This runoff not only damages the site and surrounding land, but also threatens compliance with environmental laws.
Compact soil helps by minimizing surface water infiltration and stabilizing the ground. Combined with proper grading and strategically placed drainage features, compaction ensures that rainwater moves where it should—and stays out of places it shouldn’t.
Meeting EPA Requirements
The Environmental Protection Agency (EPA) enforces regulations that cover stormwater management and erosion control on construction sites. For oil and gas companies, this means using best practices like silt fences, sediment basins, and vegetative buffers—but it also means starting with the basics: solid, compacted soil.
When inspectors arrive onsite, they’re not just looking for paperwork. They want to see visible efforts to control runoff and stabilize the land. Well-compacted soil shows that a pipeline company or contractor takes these requirements seriously.
From Land Clearing to Final Grading: Soil Matters
Environmental compliance starts before the first pipe is laid. During land clearing, crews should consider how removing vegetation will affect soil structure. From there, compact soil must be carefully planned into every phase of construction:
• Pad Construction That Resists Washout
A well-compacted pad means engineering a foundation that can withstand heavy loads and unpredictable weather. Without proper compaction, rainwater can seep into loose soil, eroding the subgrade and undermining structural integrity. This leads to washouts, soft spots, and eventually unsafe working conditions for personnel and equipment. When compact soil is part of pad construction, it improves water runoff management, keeps foundations firm, and extends the life of the site—especially critical in oilfield construction where downtime equals lost productivity. Whether it’s supporting pump jacks, tank batteries, or production facilities, a pad built on solid, compacted ground is built to last.
• Infrastructure Like Drilling Rigs and Compressor Stations That Remain Stable
Drilling rigs and compressor stations require rock-solid footing. These structures generate intense vibrations, support heavy vertical loads, and must maintain precise alignment—none of which is possible if the ground beneath them shifts or settles unevenly. Compact soil reduces the risk of settlement over time, providing a stable base that minimizes stress on support structures and anchoring systems. In compressor station construction, for example, uneven soil can lead to pipe misalignment, vibration damage, or even system shutdowns. Investing in proper compaction ensures that infrastructure stays aligned, secure, and fully operational—day in and day out.
• Access Roads That Won’t Become Rutted Channels After a Storm
Access roads are often the lifeline of a remote construction site, used daily by heavy equipment, delivery trucks, and crews. Without compacted subgrades and proper drainage, these roads quickly become muddy, rutted channels when hit by rain. That leads to stuck equipment, site delays, and higher maintenance costs. When roads are built on compact soil with the right slope and grading, they shed water efficiently, maintain a smooth driving surface, and stay operational through changing weather. The goal is to ensure safe, consistent access that keeps the entire operation moving forward.
And for projects involving frac pond construction or hydrostatic testing, soil stability becomes even more important. You need soil that holds up under pressure, retains water when required, and channels it away when necessary.
XCU’s Approach to Soil and Compliance
At Xccelerated Construction Unlimited (XCU), compact soil is more a step on the path; it's a foundation for long-term performance and environmental stewardship. Our crews understand how to grade, compact, and reinforce soil to meet both structural and environmental goals.
We own and operate our own equipment, which means we can act quickly, adapt to field conditions, and deliver consistent results. Whether we’re handling oilfield construction, pad preparation, or pipeline repair, we focus on doing the job right the first time. That includes:
• Tailoring Compaction Methods to Soil Type
Not all soil behaves the same, and trying to treat it like it does is a recipe for failure. Sandy soils, for example, drain well but can be unstable unless compacted properly. Clay soils hold moisture, which makes them swell and shrink—posing challenges for maintaining density. At XCU, we assess soil composition upfront to select the right compaction technique and equipment. That might mean using vibratory rollers for granular soils, sheepsfoot compactors for cohesive clays, or adjusting moisture content to achieve optimal density. Tailoring the approach ensures we’re not just meeting compaction specs—we’re creating a solid, long-lasting base suited to the terrain and the demands of the project, whether it’s pad construction, land clearing, or pipeline installation.
• Coordinating with Environmental Engineers
Compaction and environmental protection go hand-in-hand. Our team works directly with environmental engineers to ensure that our dirt work supports erosion control plans, sediment runoff prevention, and site drainage requirements. For instance, compacted soil must support—not hinder—stormwater management systems, and it shouldn’t interfere with wetlands, watersheds, or sensitive habitats. By collaborating early, we can ensure that compaction enhances both structural integrity and environmental compliance. It’s a partnership that keeps our work aligned with EPA guidelines, site permits, and long-term sustainability goals.
• Prioritizing Compliance from the Planning Phase Onward
Compliance can’t be an afterthought. That’s why we build it into the project from day one—especially when it comes to soil compaction. We start with a full review of local, state, and federal regulations, then use that to guide everything from soil testing and compaction strategy to site inspections and documentation. This proactive approach helps avoid delays due to non-compliance, keeps inspectors satisfied, and protects our clients from costly rework or fines. In industries like oil and gas construction, where regulatory scrutiny is high and environmental risks are real, it pays to get it right from the start.
The Bottom Line
In oil and gas construction, every successful project starts with stable ground. And in today’s regulatory environment, compact soil isn’t just good practice—it’s essential.
From pipeline construction and inspection to building infrastructure like compressor stations and frac ponds, soil compaction helps protect the environment, reduce liability, and keep projects moving forward.